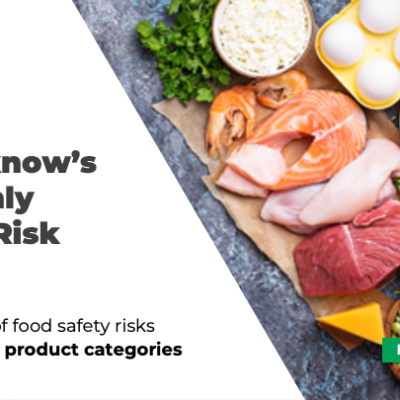
Integrating High-Quality Food Safety Insights into Risk Prevention Workflows
Last week, Agroknow and FOODAKAI held an insightful webinar on the integration of high-quality food risk intelligence data into the workflows of food & beverage companies in order to enhance risk prevention.
The webinar’s host, Marina Bifsha, Head of Customer Success was joined by Mihalis Papakostandinou, Head of Data Team at Agroknow, aimed to tackle the question of how can external food safety risk data can be seamlessly integrated into the risk mitigation plans food & beverage companies with the help of AI.
Among the topics that were discussed were:
- workflows employed by major players in the food and beverage manufacturing industry to perform food risk intelligence,
- procedures that these companies follow to utilize the integrated global data in the decision making processes,
- Concrete use cases of how FOODAKAI's food risk intelligence and predictive analytics platform can be effectively integrated into the workflow of such companies to support proactive risk prevention.
Key Takeaways
During the 1-hour discussion between the panelists, they went on to discuss about 3 distinct workflows utilized by food & beverage manufacturers as well as retailers in order to integrate external data and perform risk assessment and communicate such insights with their teams, as well as 3 practical uses cases on how these workflows can benefit from improved automation through AI and predictive analytics, incorporating forecasting to drastically enhance risk mitigation decision making.
What was most highlighted was:
- The importance of easy deployment of food safety risk solutions into the workflows of food companies.
- The need for data curation and harmonization crucial for decision making
- Seamless data aggregation & integration of all relevant sources & streams in internal workflows, and reducing time spent collecting relevant information about hazard, risks & suppliers from various web sites, voted as the most pressing challenges.
3 Workflow Use Cases
1. Generating & Storing Tailor-made reports on supply chain to share with relevant stakeholders
Many food & beverage companies compile complex monthly reports on individual ingredients & suppliers which they later analyze and correlate into actionable insights to distribute them to relevant teams. With these reports they often try to develop trends and forecasts every month and also share them with each plant manager to set the appropriate preventive measures in place.
With FOODAKAI, food & beverage companies can customize the platform to provide aggregated food risk intelligence for their own supply chain, including risk geographies areas and sourcing suppliers. Through daily email alerts they can continuously monitor their supply chain in rea-time and be updated on all emerging risks.
2. Have a harmonized view of their internal & external data in a single dashboard
Food & beverage retailers often utilize a number of horizon scanning tools in order to export food safety data analytics on finished products, hazards & suppliers which they then provide to their store managers worldwide to take appropriate preventive measures.
Utilizing FOODAKAI, food & beverage companies can have aggregated overview of all external and internal information in a single unified environment, including supplier's risk performance. This way they can identify supplier's risks relevant to their sourced ingredients.
Additionally they can have their internal lab test results integrated into the FOODAKAI platform, or in other BI tools or internal dashboards, and correlated and combined with external information to generate lab test results insights for specific regions or hazards.
3. Integrated Forecasts in internal workflow
With new food safety incidents announced every other day, food & beverage companies realize that they need to be able to anticipate new risks in their supply chain. With FOODAKAI’s highly accurate forecasts, food & beverage companies can identify potential hazards and take the necessary mitigation measures to prevent recalls. In addition, they can plan and intensify the supplier audits based on the forecasted risks in a region by checking and updating the lab testing plan according to emerging risks and be always one step ahead.
Watch the full discussion here.
Want to receive helpful food safety intelligence in your inbox?
Funding for this research has been provided by the European Union’s Horizon Europe research and innovation programme EFRA (Grant Agreement Number 101093026). Funded by the European Union. Views and opinions expressed are however those of the author(s) only and do not necessarily reflect those of the European Union or European Commission-EU. Neither the European Union nor the granting authority can be held responsible for them.