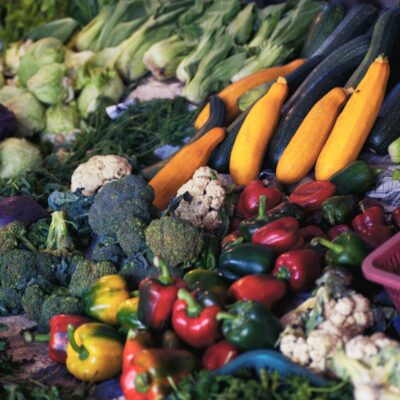
Don’t Get Siloed: Why Aggregated Laboratory Testing Data Analytics are key to Preventing Costly Recalls
In the fast-paced and highly-regulated food industry, ensuring the safety and quality of products is paramount. However, many food companies still operate with fragmented data management systems, manual processes, and outdated risk management practices. This fragmented approach poses significant risks, including the potential for costly recalls. Harmonized testing data and aggregated analytics offers a solution, providing food safety leaders with the insights they need to mitigate threats effectively.
The Pitfalls of Fragmented Data Management Systems
Many food manufacturers operate multiple production facilities across different locations, each with their own lab testing equipment and database. This results in data silos that make it challenging to access comprehensive information. For example, a food manufacturer with several production sites may have testing data stored in separate databases, preventing a holistic view of the company's overall food safety and quality status. Without harmonized data, identifying trends and emerging risks becomes difficult, leaving the company vulnerable to undetected threats.
The Inefficiencies of Manual Processes
Reliance on manual data entry and processing of files slows down workflows and increases the risk of errors. Consider a food manufacturer that needs to manually extract important data and KPIs from numerous certificates of analysis and excel files extracted from laboratory information systems. This is a process prone to human error. Such inefficiencies can delay the identification of potential issues, increasing the likelihood of contaminated products reaching consumers.
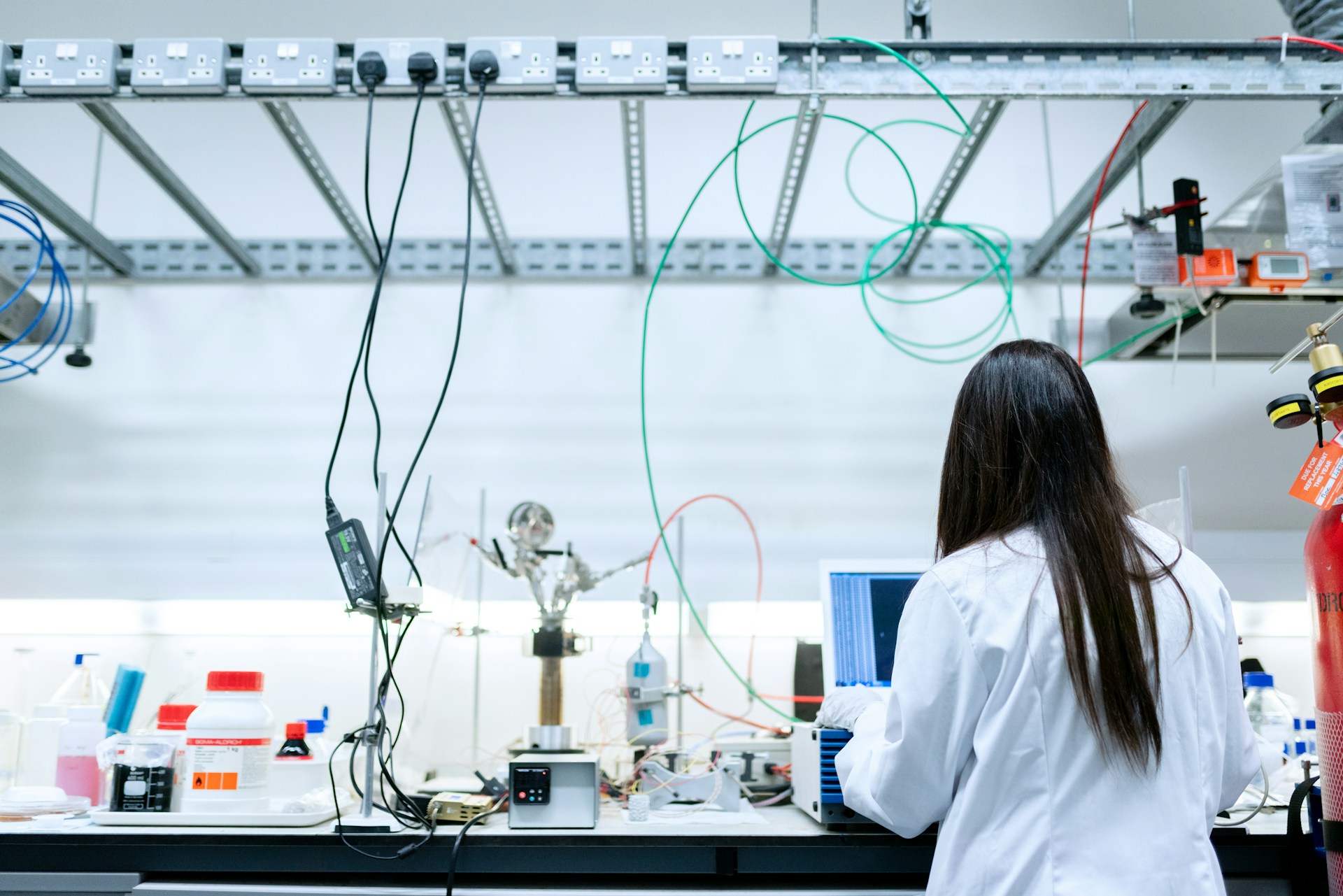
The Need for Proactive Risk Management and Real-Time Monitoring
Without real-time monitoring and proactive risk management, food companies may struggle to detect emerging risks and respond swiftly to potential issues. For instance, a food manufacturer that sends samples to external labs for analysis may face several days of waiting for results. This delay can prevent timely responses to contamination and quality issues, leading to product recalls and significant financial losses.
The Challenge of Integrating Different Data Sources
Food companies often invest in various software solutions over the years, resulting in different systems to store information across departments and locations. Incompatibility between these systems and data formats complicates information exchange and collaboration. To collect all this data in a central location companies have invested in setting up data lakes which solves only part of the problem, but the data is not harmonized. For example, a company might have different lab systems that save data in incompatible formats, making it difficult to gain a unified view of food safety metrics. This lack of integration hampers the ability to make informed decisions and respond to risks promptly.
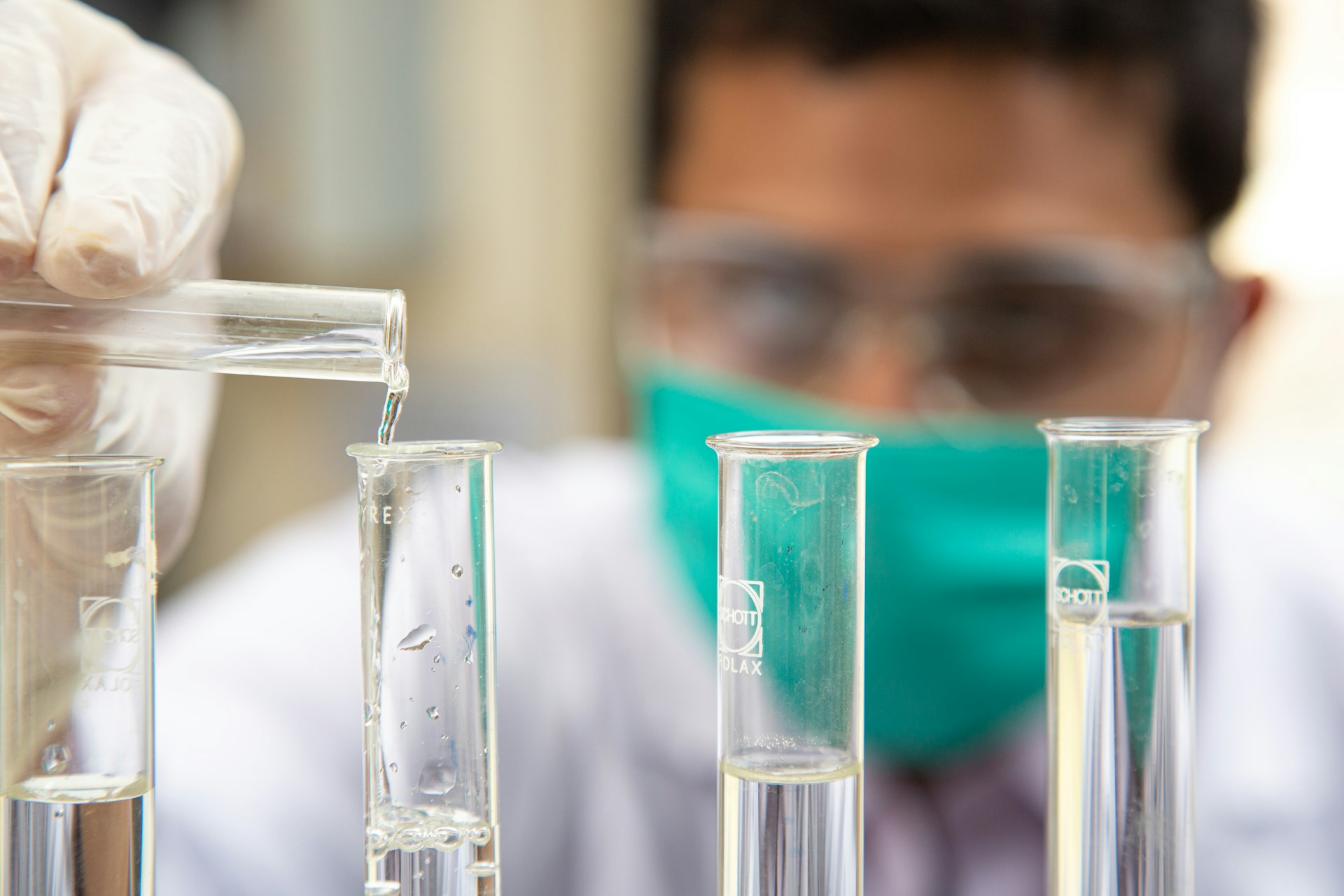
Harmonized testing data and Aggregated Analytics
Harmonized testing data and aggregated analytics address these challenges by consolidating data from disparate sources into a unified dashboard. This holistic view enables food safety leaders to identify trends, spot potential risks early, and implement corrective actions before issues escalate. With real-time data access and advanced analytical tools, companies can move from reactive to proactive food safety management.
By harmonizing testing data and adopting aggregated analytics in their workflows, food companies can:
- Enhance Data Accessibility: Eliminate data silos and provide a comprehensive view of food safety across all production sites.
- Improve Accuracy and Efficiency: Reduce reliance on manual processes, minimizing errors and speeding up data analysis.
- Enable Real-Time Monitoring: Detect and respond to risks swiftly, preventing contamination from reaching consumers.
- Facilitate Integration: Ensure compatibility between different systems and data formats, promoting seamless information exchange and collaboration.
For food safety leaders in large food businesses, the harmonization of the fragmented laboratory testing data and the adoption of aggregated analytics is not just a technological upgrade—it's a strategic imperative. Without these insights, companies risk missing critical threats that could lead to costly recalls and damage to their reputation. By investing in data harmonization and aggregated analytics, food companies can enhance their food safety protocols, protect their brand, and ensure the highest quality products for consumers.
We work with food companies on analyzing, mapping and processing their various lab testing data types and formats in order to deliver them as a harmonized and aggregated data set or data stream (via an API) that can be integrated into internal dashboards/systems.
Would you like to learn more on how you can use your fragmented testing data to prevent incidents? Book a call today.
Want to receive helpful food safety intelligence in your inbox?