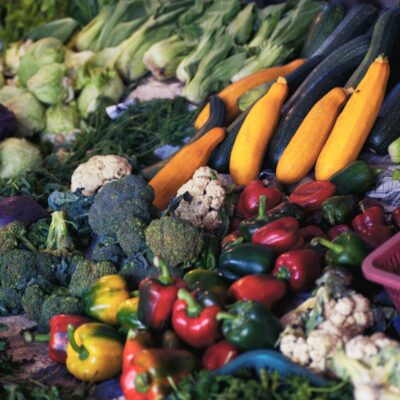
Ensure compliance in the supply chain — are digital audits a solution?
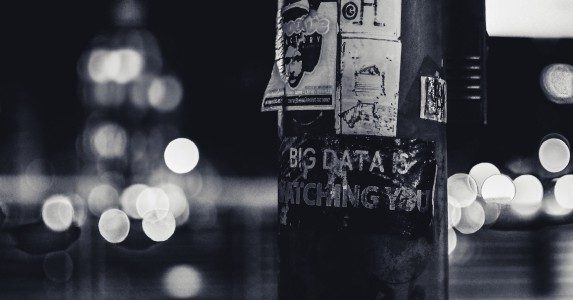
The continuously evolving supply chains need adaptive frameworks that allow for timely responses to food safety problems and moving from reaction to prevention.
What if we could perform remote supplier risk assessments and predict what will be the next critical incident in the supply chain?
A wide variety of tools is used today by Food Safety and Quality Assurance professionals to assess risk ranging from literature-based classification of risks to Excel files and software tools.
There is a huge amount of data that exists on the potential hazards and risks across the supply chain, and in some previous articles, we wrote on the types of hazards and the many tools available to food safety professionals, to monitor the risks of the supply chain.
What we want to focus on in this article is something that is often overlooked by food safety professionals regarding the supplier risk assessment process.
Increasingly, consumers are becoming more conscious of where their daily products are originating from, and food safety professionals have a duty of care to ensure that each and every product out there and the related ingredients are at the highest possible standards — sustainably and ethically sourced.
Most quality assurance and food safety professionals have their way to audit their suppliers, however, we have produced a checklist to help support this process drawing on our knowledge of the best practices.
Ensuring supplier compliance
Before embarking on a supplier risk assessment let’s go through some of the basics prior to honing in on the finer details.
· Firstly, what are the legal demands of the product category and/or raw material you are sourcing from your supplier? Is the supplier complying with these?
· Do you have access to laboratory test results for at least two batches of this product/raw material?
· Do you have test results for sensory evaluation?
· Do you have access to the global trends in recalls in this product category and/or raw material for the next 5 to 10 years?
· Have you identified the top hazards and vulnerabilities for this product category for the last 10 years?
We would recommend if there is at least one area that you don’t feel confident about you continue to read our 5-step checklist, to ensure you have peace of mind across your supply chain.
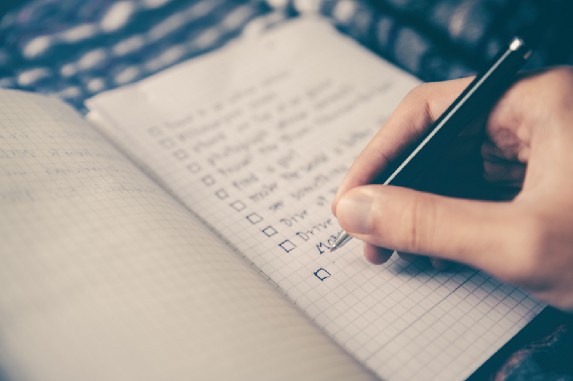
Five-step checklist
Step 1: Geopolitical considerations
· Is the supplier based in a country with a history of frequent of food recalls for this type of raw material during the last 5 years?
· Is the food safety regulatory system in the country of origin based on Codex principles or considered to be a “similar” system to the US?
· Is the supplier based in a country with a high corruption index?
· Is the supplier based in a country with a high-risk index, according to OECD?
· Is the supplier based in a country that has experienced significant fluctuations in crop production during the past 5 years?
Step 2: Supply chain due diligence
· Does the supplier provide verified information on raw material transparency?
· Does the supplier provide verified information on raw material traceability?
· Does the supplier provide verified information on raw material certification compliance?
Step 3: Certification status
· Does the supplier possess a valid certificate of compliance to a global standard of food safety such as GFSI?
· What is the status of the certificate?
· Does the supplier possess more than one food safety certification?
Step 4: History of food recalls, food safety incidents, or food fraud incidents
· Has the supplier been involved in food recalls, food safety, or food fraud incidents during the last 5 years?
· Has the supplier been involved in food recalls, food safety, or food fraud incidents during the last 2 years?
Step 5: History of border rejections, import detentions, complaints, or warning letters
· Does the supplier have any records of border rejections, import detentions, complaints, or warning letters in the last 5 years
· Does the supplier have any records of border rejections, import detentions, complaints, or warning letters in the last 2 years?
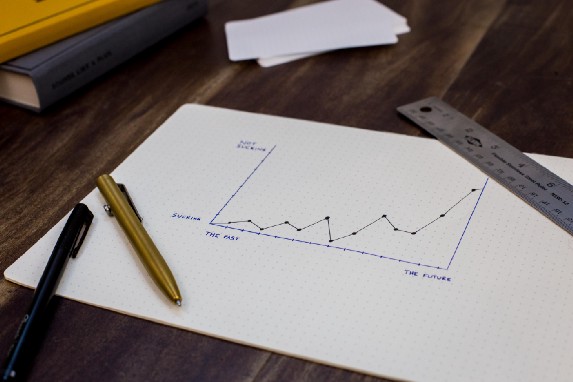
Collecting all the required information, organizing it in a spreadsheet, analyzing all the hazards, estimating the risk, and creating the report from the findings is a time-consuming and error-prone process
Today, such a process can be highly facilitated using digital platforms that provide insights into all potential hazards and allows the generation of risk reports based on data collected from a large number of National Authorities from all around the globe.
A deep hazards analysis, the supplier check, and the risk estimation can be performed efficiently and in a few minutes.
If you’d like to discover how FOODAKAI can help your Food Safety & Quality team prevent product recalls by monitoring & predicting risks, schedule a call with us!