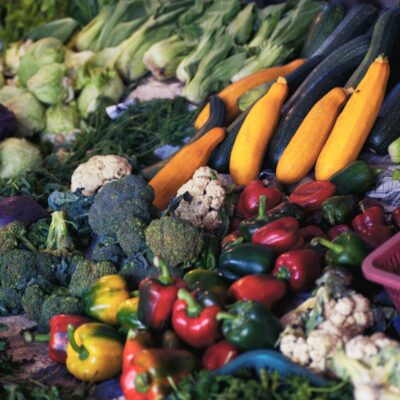
Supplier Risk Assessment and Evaluation: How to optimize processes for your FS/FQ team
Monitoring the food safety performance of collaborating suppliers can be a daunting and time-consuming task due to the sheer volume of sourcing partners, their global location, the different sourced ingredients, as well as the different food safety processes, often not digitalized employed by each of them. This can result in having a limited view of their suppliers’ food safety risk, potentially leaving them exposed to a future recall.
As food & beverage companies are increasingly asking for a way to optimize this process, Agroknow and FOODAKAI hosted an informative webinar on supplier assessment and evaluation and how time-consuming processes can be optimized according to each team’s needs.
Chrysi Soultogianni, Business Development Manager at Agroknow, invited Vishwanath Nadakalasi, Global FSQS Manager at Griffith Foods WW Inc., and Zacharoula Theodorakopoulou, Food Safety Data Curation Manager at Agroknow to discuss:
- The challenges that F&B companies need to address to perform supplier assessment.
- The deployment of new technologies and AI in these processes.
- 3 Practical use cases on:
- Evaluating & assessing potential new suppliers based on their food safety history and food safety performance risk scoring.
- Continuously monitoring suppliers’ risk performance, including all recent food safety incidents involved.
- Assessing suppliers based on sourcing ingredients risk, their geography, and ingredients future risk.
Watch the full discussion here.
Key Takeaways
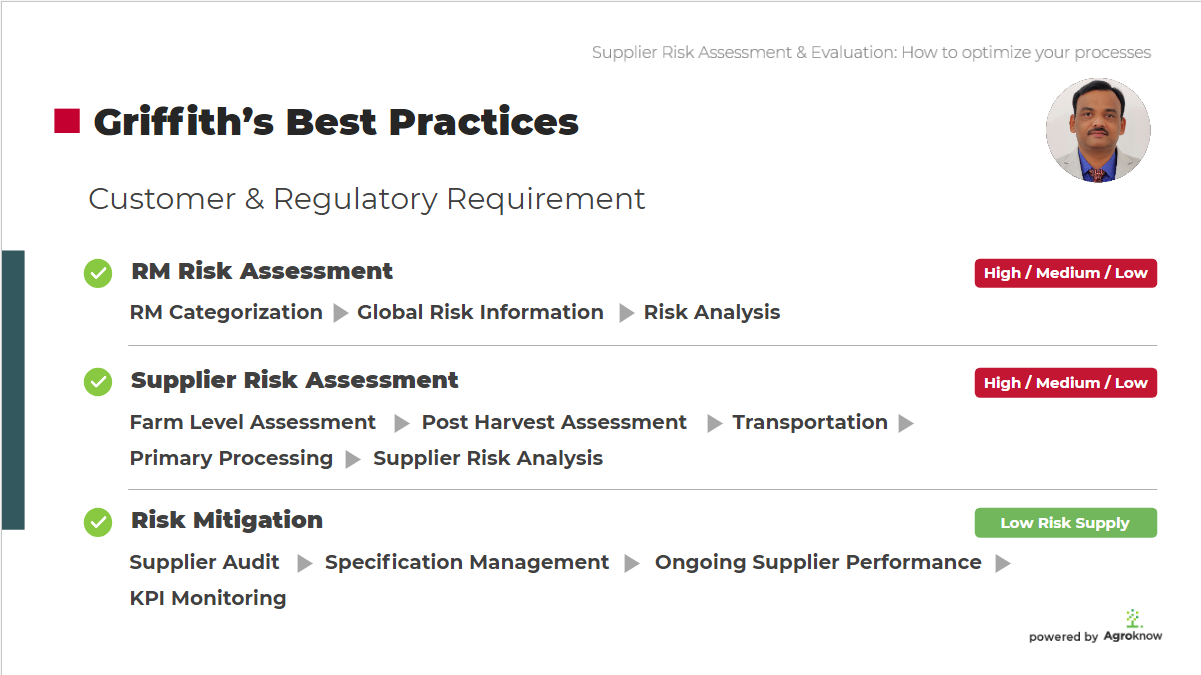
During the lively discussion, what was most highlighted was:
- The importance of supplier assessment & monitoring to:
- Stay compliant with food safety regulations
- Continuously monitor supplier performance
- Incorporate continuous supplier assessment in the HACCP Plan
- Maintain product safety, quality, and brand reputation.
- 46% of the webinar’s audience voted that monitoring supplier performance and incidents is most important when performing supplier risk assessment, followed by having an overview of their sourcing supplier’s food safety history by 38%.
- Best practices for supplier assessment such as: a) use multi-criteria evaluation, b) define key performance indicators, c) conduct a mix of scheduled and surprise audits, d) RM Risk Assessment
- Leveraging new technologies such as AI to avoid recalls with 3 use cases:
- Continuous Monitoring of Suppliers' Risk Performance and Recent Food Safety Incidents
- Assessing Supplier Food Safety Performance for Regulatory Compliance Requirements
- Supplier Risk Analysis: Ingredients, Geography, and Internal Parameters
Watch here.
Suppliers Assessment Use Cases
The Supplier check mechanism: a single point of reference to continuously monitor the suppliers’ risk performance including all recent food safety incidents
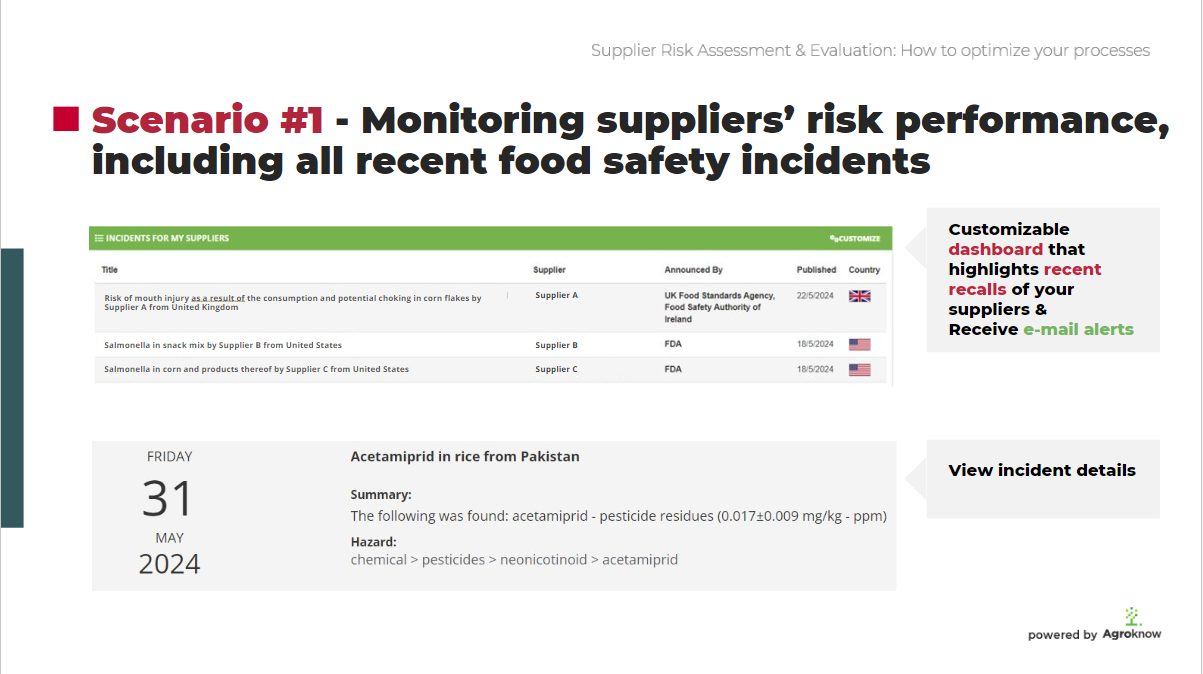
FOODAKAI’s fully customizable dashboard allows users to:
- Have a tailored view of recent recalls related to their suppliers’ network
- Receive timely and detailed alerts of new incidents
- Perform a thorough analysis of their suppliers’ historical rundown, thus being able to browse through and discover all past incidents, inspections, warning letters, etc.
The Supplier Profile tool: Evaluating & assessing potential new suppliers for compliance

- Perform an in-depth in-depth review of a new supplier based on their food safety history.
- Supplier risk assessment by factoring in countries of operation, incident & sourced ingredient risk scoring.
- Check regulatory compliance of new suppliers by evaluating their inspection history.
- collect comprehensive details on new suppliers to enhance their FSVP records.
- Know of former and recent inspections and warning letters from FDA.
Multi-factor supplier assessment
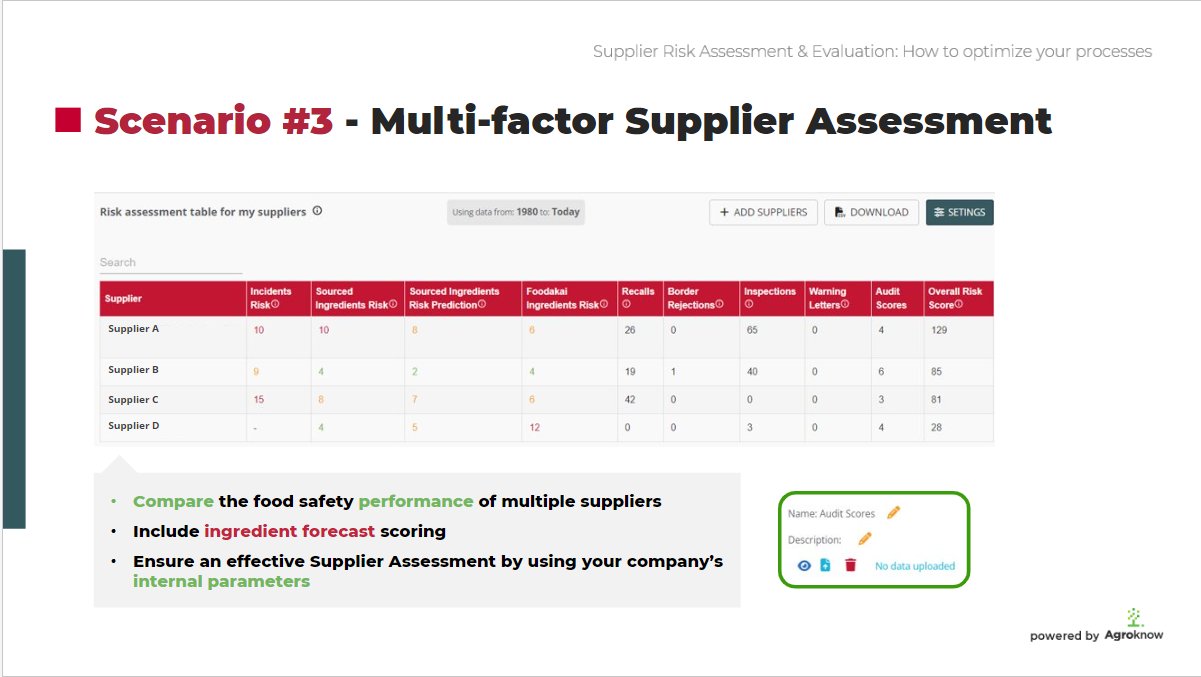
- Assess suppliers based on sourcing ingredients risk, their geography, and ingredients' future risk/
- Factor in the user’s internal parameters.
Want to see the full discussion? Watch here.
Would you be interested in watching a live demo, custom to your Supplier Risk Assessment needs and processes? Find out more.
Want to receive helpful food safety intelligence in your inbox?
Funding for this research has been provided by the European Union’s Horizon Europe innovation programme ΤΙΤΑΝ (Grant Agreement Number 101060739). Funded by the European Union. Views and opinions expressed are, however, those of the author(s) only and do not necessarily reflect those of the European Union or European Research Executive Agency. Neither the European Union nor the granting authority can be held responsible for them.